Process Management
The principles promoted by Navigate are foundational
That is, you apply them mostly by following them. No advanced degree is required, and there is no magic pill available. What we promise — and what our experience has been with leaders and individuals at companies that have followed this guidance — is that hard work, perseverance, and a willingness to take personal accountability triumphs.
There is no inherent hierarchy or “specialness” of roles in a well-functioning company. Instead, there is a commitment to serving one another by adhering to standards and processes — taking the “right action” every time, instead of creating an exception.
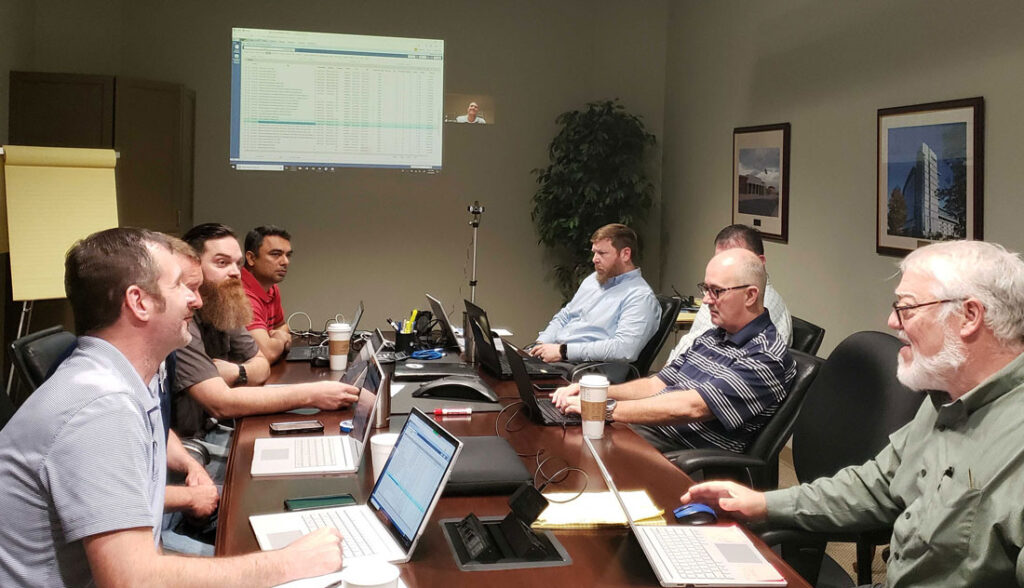
Why are standards important?
Standards are essential to the professionalization of an industry. When we follow standards, it allows us to establish, measure and assure a level of quality, and predictability to our clients, and to one another.
Quality and Standards serve as foundations of a company’s culture – whether used or not – and are essential to employee performance measurement.
Standards are critical to a company:
- In establishing a prescribed level of quality
- Creating a training curriculum for new hires and a progression through increasing skill levels
- Formalizing the company culture and brand, and
- Enabling the growth of the next generation of leadership and management.
Although there are many facets and sources of standards, it is incumbent upon the integration company and its employees to apply these standards and experience the benefits.
Lean Six Sigma
In companies where many of their projects share repeatable processes, the Lean Six Sigma principles can be used by the people closest to the work to increase efficiencies, save time and rework, reduce call-backs, and reduce “break-fix” warranty and service calls – increasing both gross and net profits.
Lean is a proven, company-wide systematic approach to eliminate / minimize waste resulting in the production of a “good” or “service” at the lowest possible cost. Lean is every system, every process, and every employee within the organization.
Every organization producing value to their clients has costs associated with designing, implementing, delivering, and servicing their intended solution. These Costs of Quality fall into two primary categories: Costs of Conformance (costs and actions taken to directly produce value to the Client) and Costs of Non-conformance (costs and actions which detract from value creation and add waste to deliverable and the process). From the Sales, Operations, and Service perspectives, any costs saved have a direct correlation to profits earned.
Applying the Principles of Lean Six Sigma to Enhance Efficiency and Increase Profits
When you look at the repeatable processes and hand-offs in your organization, you can identify and ultimately eliminate the wasteful steps. This frees up resources for more value-added efforts.
Navigate can help you:
- Understand the seven primary causes of waste and identify examples within your company
- Understand the common and special causes of process variation and their impact on productivity
- Determine 5 – 10 areas where measurable process improvements can be made in short order